Screen Printing: Printing Techniques Explained
Screen printing, also known as silk screening, is a versatile and popular printing technique that allows the transfer of vibrant, opaque colors onto a variety of materials. It is a technique that has been used for centuries, dating back to ancient China, and is still widely used today in both commercial and artistic settings. The process involves creating a stencil, or "screen," and using it to apply layers of ink on the printing surface. Each color is applied using a different stencil, one at a time, combined to achieve the final look.
The screen printing process is known for its ability to produce high-quality, durable prints with vivid colors that can withstand more stress than other Printing Techniques. It is commonly used for printing on textiles, such as t-shirts and tote bags, but can also be used on paper, wood, ceramics, and other materials. Despite the advent of digital printing technologies, screen printing remains a preferred technique for many applications due to its reliability, versatility, and cost-effectiveness.
Screen printing, also known as silk screening, is a versatile and popular printing technique that allows the transfer of vibrant, opaque colors onto a variety of materials. It is a technique that has been used for centuries, dating back to ancient China, and is still widely used today in both commercial and artistic settings. The process involves creating a stencil, or "screen," and using it to apply layers of ink on the printing surface. Each color is applied using a different stencil, one at a time, combined to achieve the final look.
The screen printing process is known for its ability to produce high-quality, durable prints with vivid colors that can withstand more stress than other Printing Techniques. It is commonly used for printing on textiles, such as t-shirts and tote bags, but can also be used on paper, wood, ceramics, and other materials. Despite the advent of digital printing technologies, screen printing remains a preferred technique for many applications due to its reliability, versatility, and cost-effectiveness.
Screen printing, also known as silk screening, is a versatile and popular printing technique that allows the transfer of vibrant, opaque colors onto a variety of materials. It is a technique that has been used for centuries, dating back to ancient China, and is still widely used today in both commercial and artistic settings. The process involves creating a stencil, or "screen," and using it to apply layers of ink on the printing surface. Each color is applied using a different stencil, one at a time, combined to achieve the final look.
The screen printing process is known for its ability to produce high-quality, durable prints with vivid colors that can withstand more stress than other Printing Techniques. It is commonly used for printing on textiles, such as t-shirts and tote bags, but can also be used on paper, wood, ceramics, and other materials. Despite the advent of digital printing technologies, screen printing remains a preferred technique for many applications due to its reliability, versatility, and cost-effectiveness.



History of Screen Printing
The origins of screen printing can be traced back to the Song Dynasty in China, where it was used as a technique of transferring designs onto fabrics. The technique was later adopted and refined by other Asian countries like Japan and India. The basic principles of screen printing have remained largely unchanged over the centuries, although the materials and equipment used have evolved significantly.
In the 20th century, screen printing gained popularity in the Western world, particularly in the realm of advertising and fine art. Artists like Andy Warhol famously used screen printing in their work, bringing the technique into the mainstream. Today, screen printing is a staple in the printing industry, used for everything from custom t-shirts and merchandise to fine art prints and posters.

The origins of screen printing can be traced back to the Song Dynasty in China, where it was used as a technique of transferring designs onto fabrics. The technique was later adopted and refined by other Asian countries like Japan and India. The basic principles of screen printing have remained largely unchanged over the centuries, although the materials and equipment used have evolved significantly.
In the 20th century, screen printing gained popularity in the Western world, particularly in the realm of advertising and fine art. Artists like Andy Warhol famously used screen printing in their work, bringing the technique into the mainstream. Today, screen printing is a staple in the printing industry, used for everything from custom t-shirts and merchandise to fine art prints and posters.

The origins of screen printing can be traced back to the Song Dynasty in China, where it was used as a technique of transferring designs onto fabrics. The technique was later adopted and refined by other Asian countries like Japan and India. The basic principles of screen printing have remained largely unchanged over the centuries, although the materials and equipment used have evolved significantly.
In the 20th century, screen printing gained popularity in the Western world, particularly in the realm of advertising and fine art. Artists like Andy Warhol famously used screen printing in their work, bringing the technique into the mainstream. Today, screen printing is a staple in the printing industry, used for everything from custom t-shirts and merchandise to fine art prints and posters.

Evolution of Screen Printing Techniques
The basic technique of screen printing has remained the same over the centuries: a design is created on a fine mesh or screen, and ink is pushed through the areas of the screen that are not blocked by the design. However, the materials and tools used in screen printing have evolved significantly. Originally, screens were made of silk, hence the term "silk screening." Today, screens are typically made of synthetic materials like polyester.
The inks used in screen printing have also evolved. Originally, natural dyes and pigments were used. Today, a wide variety of inks are available, including plastisol, water-based inks, and specialty inks like metallic, glow-in-the-dark, and puff inks. The development of these materials has expanded the possibilities of screen printing, allowing for a wider range of colors, effects, and applications.
The Screen Printing Process
The screen printing process involves several steps, each of which requires careful attention to detail. The first step is creating the design that will be printed. This design is then transferred onto a stencil or "screen." The screen is placed on the material to be printed, and ink is applied to the top of the screen. A squeegee is used to press the ink through the screen, where it adheres to the material below. The screen is then lifted, leaving the inked design on the material.
Each color in a design requires a separate screen, and the printing process is repeated for each color. The colors are applied one at a time, and the material must be carefully aligned each time to ensure that the colors line up correctly in the final design. After all colors have been applied, the material is dried or cured to set the ink.
Creating the Design
The first step in the screen printing process is creating the design that will be printed. This can be done using a variety of techniques, including hand-drawing, digital design, or photographic techniques. The design is typically created in black and white, with each color in the final design represented by a different shade of gray.
Once the design is finalized, it is transferred onto a transparent film. This film is used to create the stencil or "screen" that will be used in the printing process. The design on the film is used to block out areas of the screen, creating a negative image of the design.
Preparing the Screen
Once the design is transferred onto the film, the next step is to prepare the screen. The screen is typically made of a fine mesh stretched over a frame. The mesh is coated with a light-sensitive emulsion, and the film with the design is placed on top. The screen is then exposed to light. The light hardens the emulsion in the areas not covered by the design, creating a stencil of the design on the screen.
After the screen is exposed, it is washed with water. The water washes away the unhardened emulsion in the areas of the screen covered by the design, leaving a clear path for the ink to pass through. The screen is then dried and ready for printing.
Screen Printing Inks
There are several types of inks that can be used in screen printing, each with its own characteristics and applications. The choice of ink depends on the material being printed on, the desired look of the final print, and the specific requirements of the project.
Plastisol ink is the most commonly used type of screen printing ink. It is a PVC-based ink that is extremely durable, vibrant, and versatile. Plastisol ink does not dry in the screen, making it easy to work with, especially for beginners. However, it requires heat to cure, or dry, after it is applied to the material.
Water-Based Inks
Water-based inks are another popular choice for screen printing. As the name suggests, these inks are made with water rather than plastic or PVC. Water-based inks are thinner and more transparent than plastisol inks, allowing for a softer feel and a more vintage look. They also dry in the air, eliminating the need for a heat curing process.
However, water-based inks can be more challenging to work with than plastisol inks. They dry quickly, which can lead to clogging in the screen. They also require more layers to achieve a vibrant color, especially on darker materials. Despite these challenges, water-based inks are a popular choice for their eco-friendly properties and soft, natural feel.
Specialty Inks
In addition to plastisol and water-based inks, there are also a variety of specialty inks that can be used in screen printing. These include metallic inks, glow-in-the-dark inks, puff inks, and more. Specialty inks allow for a wide range of effects and finishes, adding a unique touch to any screen printed design.
Metallic inks contain metallic particles that give the print a shiny, reflective finish. Glow-in-the-dark inks contain phosphorescent materials that glow when exposed to light. Puff inks contain a heat-reactive component that expands when heated, creating a raised, textured effect. Each of these inks has its own specific application and curing process, and can add a unique touch to any screen printed design.

The basic technique of screen printing has remained the same over the centuries: a design is created on a fine mesh or screen, and ink is pushed through the areas of the screen that are not blocked by the design. However, the materials and tools used in screen printing have evolved significantly. Originally, screens were made of silk, hence the term "silk screening." Today, screens are typically made of synthetic materials like polyester.
The inks used in screen printing have also evolved. Originally, natural dyes and pigments were used. Today, a wide variety of inks are available, including plastisol, water-based inks, and specialty inks like metallic, glow-in-the-dark, and puff inks. The development of these materials has expanded the possibilities of screen printing, allowing for a wider range of colors, effects, and applications.
The Screen Printing Process
The screen printing process involves several steps, each of which requires careful attention to detail. The first step is creating the design that will be printed. This design is then transferred onto a stencil or "screen." The screen is placed on the material to be printed, and ink is applied to the top of the screen. A squeegee is used to press the ink through the screen, where it adheres to the material below. The screen is then lifted, leaving the inked design on the material.
Each color in a design requires a separate screen, and the printing process is repeated for each color. The colors are applied one at a time, and the material must be carefully aligned each time to ensure that the colors line up correctly in the final design. After all colors have been applied, the material is dried or cured to set the ink.
Creating the Design
The first step in the screen printing process is creating the design that will be printed. This can be done using a variety of techniques, including hand-drawing, digital design, or photographic techniques. The design is typically created in black and white, with each color in the final design represented by a different shade of gray.
Once the design is finalized, it is transferred onto a transparent film. This film is used to create the stencil or "screen" that will be used in the printing process. The design on the film is used to block out areas of the screen, creating a negative image of the design.
Preparing the Screen
Once the design is transferred onto the film, the next step is to prepare the screen. The screen is typically made of a fine mesh stretched over a frame. The mesh is coated with a light-sensitive emulsion, and the film with the design is placed on top. The screen is then exposed to light. The light hardens the emulsion in the areas not covered by the design, creating a stencil of the design on the screen.
After the screen is exposed, it is washed with water. The water washes away the unhardened emulsion in the areas of the screen covered by the design, leaving a clear path for the ink to pass through. The screen is then dried and ready for printing.
Screen Printing Inks
There are several types of inks that can be used in screen printing, each with its own characteristics and applications. The choice of ink depends on the material being printed on, the desired look of the final print, and the specific requirements of the project.
Plastisol ink is the most commonly used type of screen printing ink. It is a PVC-based ink that is extremely durable, vibrant, and versatile. Plastisol ink does not dry in the screen, making it easy to work with, especially for beginners. However, it requires heat to cure, or dry, after it is applied to the material.
Water-Based Inks
Water-based inks are another popular choice for screen printing. As the name suggests, these inks are made with water rather than plastic or PVC. Water-based inks are thinner and more transparent than plastisol inks, allowing for a softer feel and a more vintage look. They also dry in the air, eliminating the need for a heat curing process.
However, water-based inks can be more challenging to work with than plastisol inks. They dry quickly, which can lead to clogging in the screen. They also require more layers to achieve a vibrant color, especially on darker materials. Despite these challenges, water-based inks are a popular choice for their eco-friendly properties and soft, natural feel.
Specialty Inks
In addition to plastisol and water-based inks, there are also a variety of specialty inks that can be used in screen printing. These include metallic inks, glow-in-the-dark inks, puff inks, and more. Specialty inks allow for a wide range of effects and finishes, adding a unique touch to any screen printed design.
Metallic inks contain metallic particles that give the print a shiny, reflective finish. Glow-in-the-dark inks contain phosphorescent materials that glow when exposed to light. Puff inks contain a heat-reactive component that expands when heated, creating a raised, textured effect. Each of these inks has its own specific application and curing process, and can add a unique touch to any screen printed design.

The basic technique of screen printing has remained the same over the centuries: a design is created on a fine mesh or screen, and ink is pushed through the areas of the screen that are not blocked by the design. However, the materials and tools used in screen printing have evolved significantly. Originally, screens were made of silk, hence the term "silk screening." Today, screens are typically made of synthetic materials like polyester.
The inks used in screen printing have also evolved. Originally, natural dyes and pigments were used. Today, a wide variety of inks are available, including plastisol, water-based inks, and specialty inks like metallic, glow-in-the-dark, and puff inks. The development of these materials has expanded the possibilities of screen printing, allowing for a wider range of colors, effects, and applications.
The Screen Printing Process
The screen printing process involves several steps, each of which requires careful attention to detail. The first step is creating the design that will be printed. This design is then transferred onto a stencil or "screen." The screen is placed on the material to be printed, and ink is applied to the top of the screen. A squeegee is used to press the ink through the screen, where it adheres to the material below. The screen is then lifted, leaving the inked design on the material.
Each color in a design requires a separate screen, and the printing process is repeated for each color. The colors are applied one at a time, and the material must be carefully aligned each time to ensure that the colors line up correctly in the final design. After all colors have been applied, the material is dried or cured to set the ink.
Creating the Design
The first step in the screen printing process is creating the design that will be printed. This can be done using a variety of techniques, including hand-drawing, digital design, or photographic techniques. The design is typically created in black and white, with each color in the final design represented by a different shade of gray.
Once the design is finalized, it is transferred onto a transparent film. This film is used to create the stencil or "screen" that will be used in the printing process. The design on the film is used to block out areas of the screen, creating a negative image of the design.
Preparing the Screen
Once the design is transferred onto the film, the next step is to prepare the screen. The screen is typically made of a fine mesh stretched over a frame. The mesh is coated with a light-sensitive emulsion, and the film with the design is placed on top. The screen is then exposed to light. The light hardens the emulsion in the areas not covered by the design, creating a stencil of the design on the screen.
After the screen is exposed, it is washed with water. The water washes away the unhardened emulsion in the areas of the screen covered by the design, leaving a clear path for the ink to pass through. The screen is then dried and ready for printing.
Screen Printing Inks
There are several types of inks that can be used in screen printing, each with its own characteristics and applications. The choice of ink depends on the material being printed on, the desired look of the final print, and the specific requirements of the project.
Plastisol ink is the most commonly used type of screen printing ink. It is a PVC-based ink that is extremely durable, vibrant, and versatile. Plastisol ink does not dry in the screen, making it easy to work with, especially for beginners. However, it requires heat to cure, or dry, after it is applied to the material.
Water-Based Inks
Water-based inks are another popular choice for screen printing. As the name suggests, these inks are made with water rather than plastic or PVC. Water-based inks are thinner and more transparent than plastisol inks, allowing for a softer feel and a more vintage look. They also dry in the air, eliminating the need for a heat curing process.
However, water-based inks can be more challenging to work with than plastisol inks. They dry quickly, which can lead to clogging in the screen. They also require more layers to achieve a vibrant color, especially on darker materials. Despite these challenges, water-based inks are a popular choice for their eco-friendly properties and soft, natural feel.
Specialty Inks
In addition to plastisol and water-based inks, there are also a variety of specialty inks that can be used in screen printing. These include metallic inks, glow-in-the-dark inks, puff inks, and more. Specialty inks allow for a wide range of effects and finishes, adding a unique touch to any screen printed design.
Metallic inks contain metallic particles that give the print a shiny, reflective finish. Glow-in-the-dark inks contain phosphorescent materials that glow when exposed to light. Puff inks contain a heat-reactive component that expands when heated, creating a raised, textured effect. Each of these inks has its own specific application and curing process, and can add a unique touch to any screen printed design.

Applications of Screen Printing
Screen printing is a versatile printing technique that can be used on a variety of materials and for a wide range of applications. It is most commonly used for printing on textiles, such as t-shirts, sweatshirts, and tote bags. However, it can also be used on paper, wood, ceramics, glass, and even metal.
Screen printing is also used in a variety of industries. In the fashion industry, it is used to create custom clothing and accessories. In the advertising industry, it is used to create promotional products and signage. In the art world, it is used to create fine art prints and posters. The versatility and durability of screen printing make it a popular choice for many different applications.
Textile Printing
One of the most common applications of screen printing is textile printing. This includes printing on t-shirts, sweatshirts, tote bags, and other clothing and accessories. Screen printing allows for vibrant, durable prints that can withstand repeated washing and wear. It is also a cost-effective technique for large runs, making it a popular choice for custom apparel and promotional products.
Screen printing on textiles requires a special type of ink that is designed to adhere to fabric. This ink is typically thicker than the ink used for paper printing, and requires a heat curing process to set the ink and ensure its durability. The process of screen printing on textiles is similar to other forms of screen printing, but may require additional steps, such as pre-treating the fabric to ensure proper ink adhesion.
Printing on Other Materials
In addition to textiles, screen printing can also be used on a variety of other materials. This includes paper, wood, ceramics, glass, and metal. The process for printing on these materials is similar to textile printing, but may require different types of ink or additional steps to ensure proper adhesion and durability.
For example, screen printing on ceramics or glass may require a special type of ink that can withstand the high temperatures of the kiln. Similarly, screen printing on metal may require a special type of ink that is resistant to rust and corrosion. Regardless of the material, screen printing allows for vibrant, durable prints that can withstand the demands of various applications.
Screen printing is a versatile printing technique that can be used on a variety of materials and for a wide range of applications. It is most commonly used for printing on textiles, such as t-shirts, sweatshirts, and tote bags. However, it can also be used on paper, wood, ceramics, glass, and even metal.
Screen printing is also used in a variety of industries. In the fashion industry, it is used to create custom clothing and accessories. In the advertising industry, it is used to create promotional products and signage. In the art world, it is used to create fine art prints and posters. The versatility and durability of screen printing make it a popular choice for many different applications.
Textile Printing
One of the most common applications of screen printing is textile printing. This includes printing on t-shirts, sweatshirts, tote bags, and other clothing and accessories. Screen printing allows for vibrant, durable prints that can withstand repeated washing and wear. It is also a cost-effective technique for large runs, making it a popular choice for custom apparel and promotional products.
Screen printing on textiles requires a special type of ink that is designed to adhere to fabric. This ink is typically thicker than the ink used for paper printing, and requires a heat curing process to set the ink and ensure its durability. The process of screen printing on textiles is similar to other forms of screen printing, but may require additional steps, such as pre-treating the fabric to ensure proper ink adhesion.
Printing on Other Materials
In addition to textiles, screen printing can also be used on a variety of other materials. This includes paper, wood, ceramics, glass, and metal. The process for printing on these materials is similar to textile printing, but may require different types of ink or additional steps to ensure proper adhesion and durability.
For example, screen printing on ceramics or glass may require a special type of ink that can withstand the high temperatures of the kiln. Similarly, screen printing on metal may require a special type of ink that is resistant to rust and corrosion. Regardless of the material, screen printing allows for vibrant, durable prints that can withstand the demands of various applications.
Screen printing is a versatile printing technique that can be used on a variety of materials and for a wide range of applications. It is most commonly used for printing on textiles, such as t-shirts, sweatshirts, and tote bags. However, it can also be used on paper, wood, ceramics, glass, and even metal.
Screen printing is also used in a variety of industries. In the fashion industry, it is used to create custom clothing and accessories. In the advertising industry, it is used to create promotional products and signage. In the art world, it is used to create fine art prints and posters. The versatility and durability of screen printing make it a popular choice for many different applications.
Textile Printing
One of the most common applications of screen printing is textile printing. This includes printing on t-shirts, sweatshirts, tote bags, and other clothing and accessories. Screen printing allows for vibrant, durable prints that can withstand repeated washing and wear. It is also a cost-effective technique for large runs, making it a popular choice for custom apparel and promotional products.
Screen printing on textiles requires a special type of ink that is designed to adhere to fabric. This ink is typically thicker than the ink used for paper printing, and requires a heat curing process to set the ink and ensure its durability. The process of screen printing on textiles is similar to other forms of screen printing, but may require additional steps, such as pre-treating the fabric to ensure proper ink adhesion.
Printing on Other Materials
In addition to textiles, screen printing can also be used on a variety of other materials. This includes paper, wood, ceramics, glass, and metal. The process for printing on these materials is similar to textile printing, but may require different types of ink or additional steps to ensure proper adhesion and durability.
For example, screen printing on ceramics or glass may require a special type of ink that can withstand the high temperatures of the kiln. Similarly, screen printing on metal may require a special type of ink that is resistant to rust and corrosion. Regardless of the material, screen printing allows for vibrant, durable prints that can withstand the demands of various applications.
Advantages and Disadvantages of Screen Printing
Like any printing technique, screen printing has its advantages and disadvantages. Understanding these can help you determine whether screen printing is the right technique for your project.
One of the main advantages of screen printing is its versatility. It can be used on a wide range of materials, from textiles to ceramics to metal. It is also capable of producing vibrant, opaque colors that can withstand more stress than other Printing Techniques. This makes it a popular choice for applications that require durability, such as t-shirts and promotional products.
Advantages of Screen Printing
Another advantage of screen printing is its cost-effectiveness for large runs. While the setup process for screen printing can be time-consuming and costly, the cost per unit decreases significantly with larger quantities. This makes screen printing a cost-effective choice for large orders.
Screen printing is also known for its ability to reproduce vibrant colors and crisp lines. This makes it a popular choice for designs that require high levels of detail or contrast. Additionally, screen printing allows for a greater thickness of the ink than other Printing Techniques, resulting in a more tactile and vibrant print.
Disadvantages of Screen Printing
Despite its many advantages, screen printing also has its disadvantages. One of the main disadvantages is the time and cost associated with setup. Each color in a design requires a separate screen, and setting up these screens can be time-consuming. This makes screen printing less cost-effective for small runs or designs with many colors.
Another disadvantage of screen printing is that it is not ideal for reproducing photographs or complex multicolor designs. While it is possible to screen print these types of designs, it requires advanced techniques and can be more costly. Additionally, screen printing does not allow for color gradients; each color must be printed as a solid block.
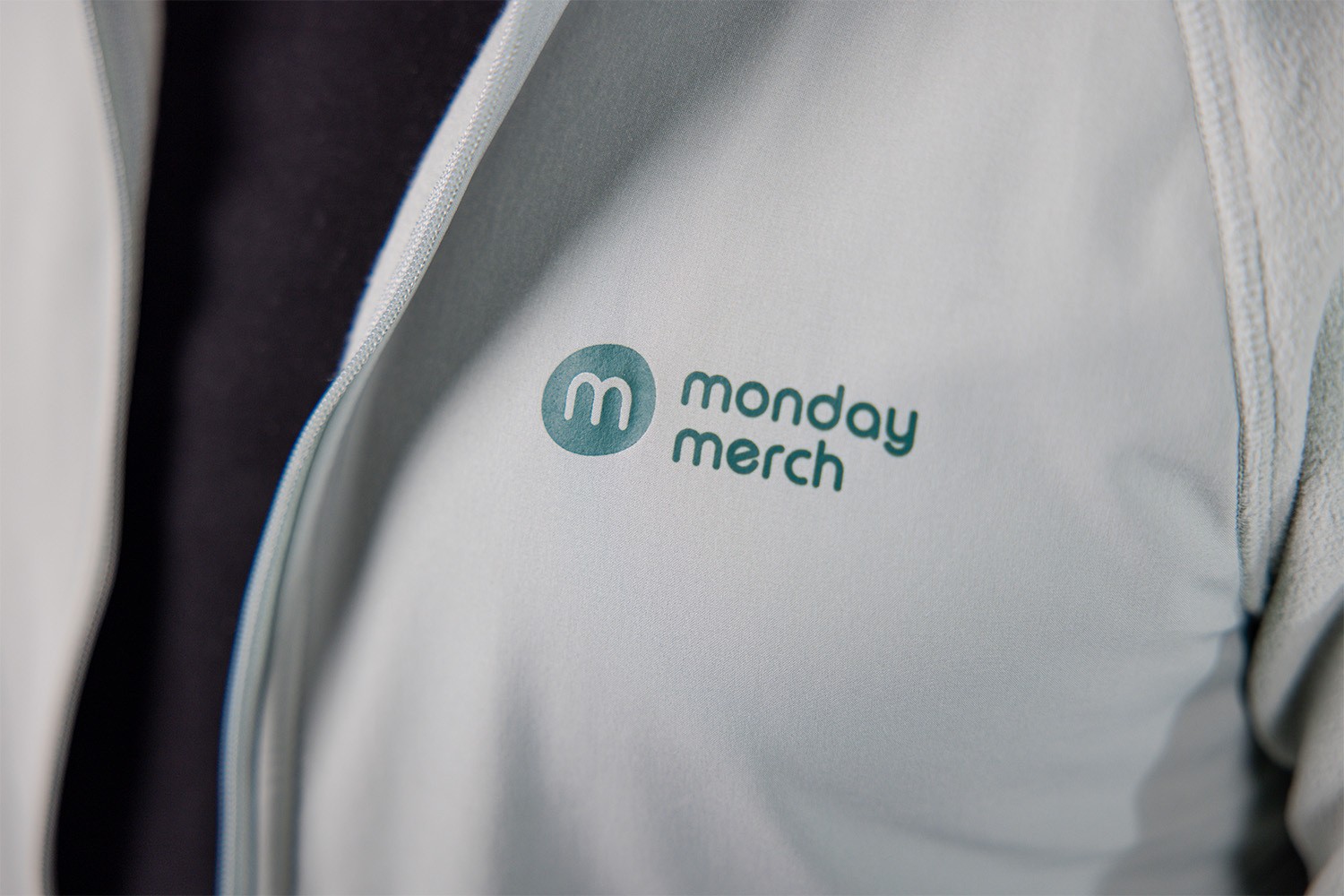
Like any printing technique, screen printing has its advantages and disadvantages. Understanding these can help you determine whether screen printing is the right technique for your project.
One of the main advantages of screen printing is its versatility. It can be used on a wide range of materials, from textiles to ceramics to metal. It is also capable of producing vibrant, opaque colors that can withstand more stress than other Printing Techniques. This makes it a popular choice for applications that require durability, such as t-shirts and promotional products.
Advantages of Screen Printing
Another advantage of screen printing is its cost-effectiveness for large runs. While the setup process for screen printing can be time-consuming and costly, the cost per unit decreases significantly with larger quantities. This makes screen printing a cost-effective choice for large orders.
Screen printing is also known for its ability to reproduce vibrant colors and crisp lines. This makes it a popular choice for designs that require high levels of detail or contrast. Additionally, screen printing allows for a greater thickness of the ink than other Printing Techniques, resulting in a more tactile and vibrant print.
Disadvantages of Screen Printing
Despite its many advantages, screen printing also has its disadvantages. One of the main disadvantages is the time and cost associated with setup. Each color in a design requires a separate screen, and setting up these screens can be time-consuming. This makes screen printing less cost-effective for small runs or designs with many colors.
Another disadvantage of screen printing is that it is not ideal for reproducing photographs or complex multicolor designs. While it is possible to screen print these types of designs, it requires advanced techniques and can be more costly. Additionally, screen printing does not allow for color gradients; each color must be printed as a solid block.
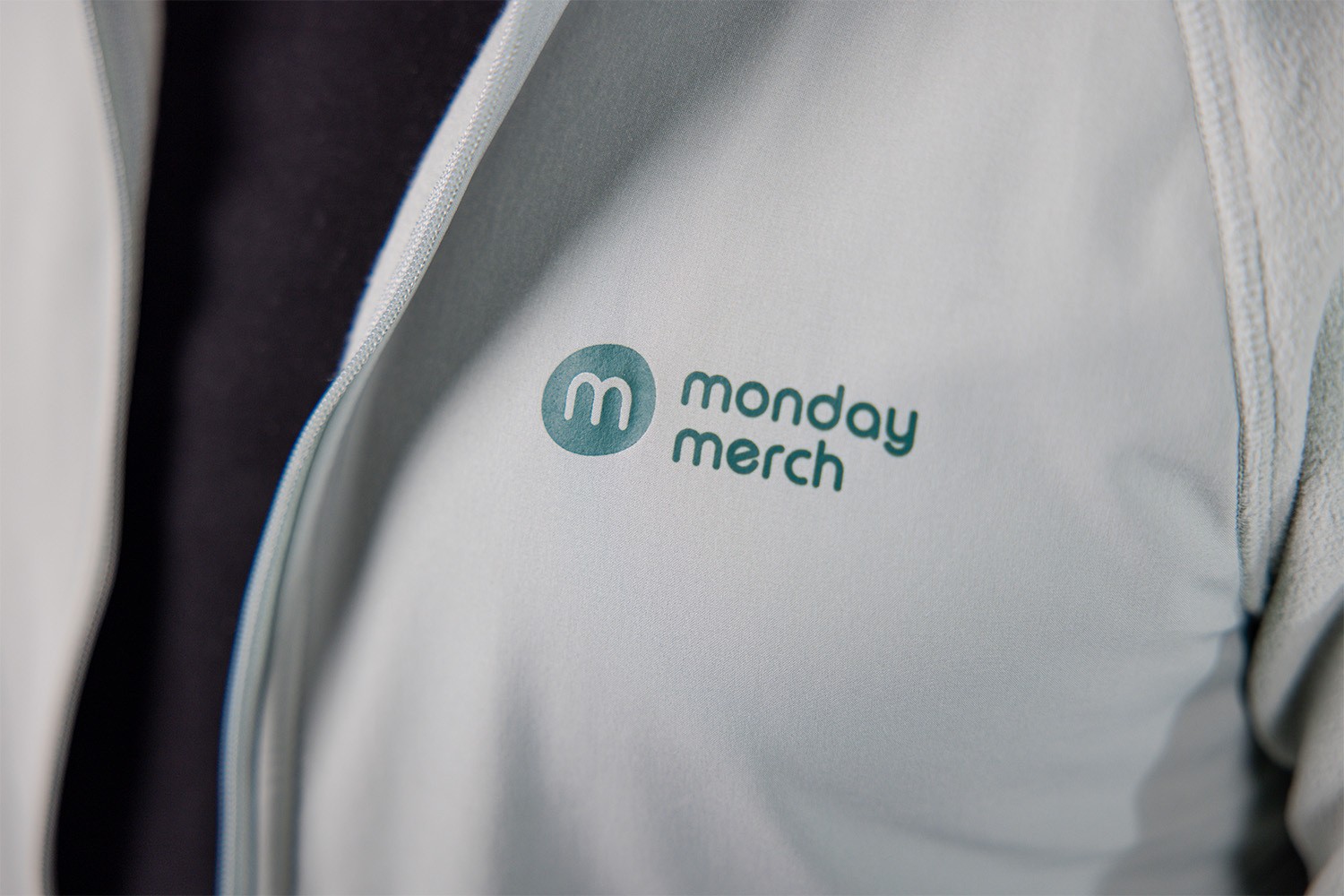
Like any printing technique, screen printing has its advantages and disadvantages. Understanding these can help you determine whether screen printing is the right technique for your project.
One of the main advantages of screen printing is its versatility. It can be used on a wide range of materials, from textiles to ceramics to metal. It is also capable of producing vibrant, opaque colors that can withstand more stress than other Printing Techniques. This makes it a popular choice for applications that require durability, such as t-shirts and promotional products.
Advantages of Screen Printing
Another advantage of screen printing is its cost-effectiveness for large runs. While the setup process for screen printing can be time-consuming and costly, the cost per unit decreases significantly with larger quantities. This makes screen printing a cost-effective choice for large orders.
Screen printing is also known for its ability to reproduce vibrant colors and crisp lines. This makes it a popular choice for designs that require high levels of detail or contrast. Additionally, screen printing allows for a greater thickness of the ink than other Printing Techniques, resulting in a more tactile and vibrant print.
Disadvantages of Screen Printing
Despite its many advantages, screen printing also has its disadvantages. One of the main disadvantages is the time and cost associated with setup. Each color in a design requires a separate screen, and setting up these screens can be time-consuming. This makes screen printing less cost-effective for small runs or designs with many colors.
Another disadvantage of screen printing is that it is not ideal for reproducing photographs or complex multicolor designs. While it is possible to screen print these types of designs, it requires advanced techniques and can be more costly. Additionally, screen printing does not allow for color gradients; each color must be printed as a solid block.
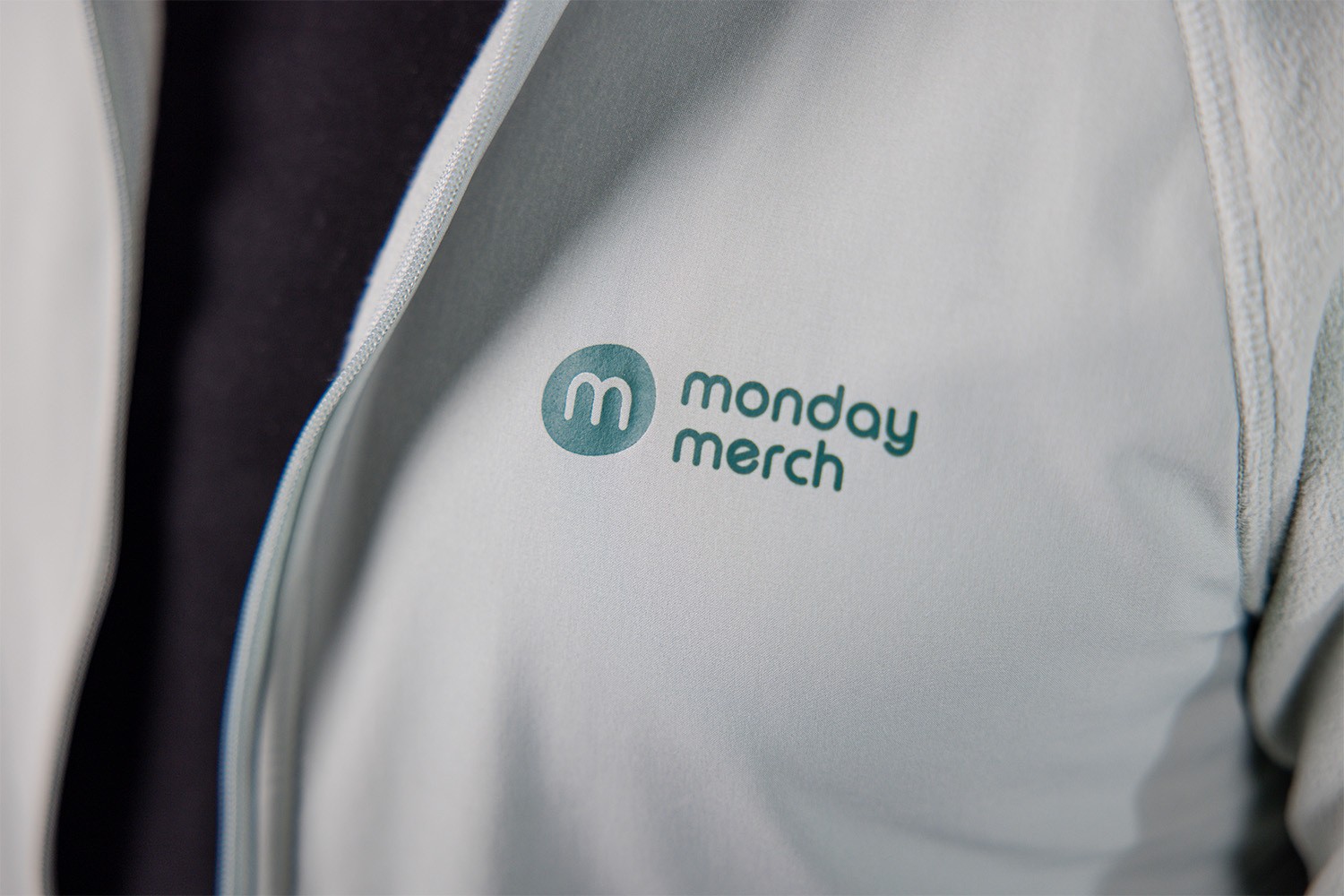
Conclusion
In conclusion, screen printing is a versatile and popular printing technique that offers many advantages. It is capable of producing vibrant, durable prints on a wide range of materials, making it a popular choice for many applications. However, it also has its disadvantages, and may not be the best choice for every project.
Whether you are a designer looking to create custom apparel, an artist looking to reproduce your work, or a business owner looking to create promotional products, understanding the screen printing process can help you make informed decisions about your printing needs. With its rich history, versatile applications, and wide range of possibilities, screen printing is a valuable tool in the world of printing and design.
In conclusion, screen printing is a versatile and popular printing technique that offers many advantages. It is capable of producing vibrant, durable prints on a wide range of materials, making it a popular choice for many applications. However, it also has its disadvantages, and may not be the best choice for every project.
Whether you are a designer looking to create custom apparel, an artist looking to reproduce your work, or a business owner looking to create promotional products, understanding the screen printing process can help you make informed decisions about your printing needs. With its rich history, versatile applications, and wide range of possibilities, screen printing is a valuable tool in the world of printing and design.
In conclusion, screen printing is a versatile and popular printing technique that offers many advantages. It is capable of producing vibrant, durable prints on a wide range of materials, making it a popular choice for many applications. However, it also has its disadvantages, and may not be the best choice for every project.
Whether you are a designer looking to create custom apparel, an artist looking to reproduce your work, or a business owner looking to create promotional products, understanding the screen printing process can help you make informed decisions about your printing needs. With its rich history, versatile applications, and wide range of possibilities, screen printing is a valuable tool in the world of printing and design.
How Monday Merch can help you
With Monday Merch, we design, produce, warehouse and distribute merchandise globally. You simply select the products and we do everything else, starting with free designs and a quote in 24 hours. Our mission is to make merch easy!
With Monday Merch, we design, produce, warehouse and distribute merchandise globally. You simply select the products and we do everything else, starting with free designs and a quote in 24 hours. Our mission is to make merch easy!
With Monday Merch, we design, produce, warehouse and distribute merchandise globally. You simply select the products and we do everything else, starting with free designs and a quote in 24 hours. Our mission is to make merch easy!
Table of Contents
Stay up to date
Stay up to date
Stay up to date
Other Printing Techniques
Other Printing Techniques
Learn more about other printing techniques